现代半导体制造的目标是为便携式产品开发具有越来越小和更薄封装的电子设备。实现这一目标最重要的步骤之一是通过机械研磨工艺将加工后的硅晶片从背面减薄至 50μm 以下。为了避免应力和亚表面损伤,这对表面粗糙度要求非常高,在最终研磨步骤中,该粗糙度可能在 1 nm Ra 的范围内。
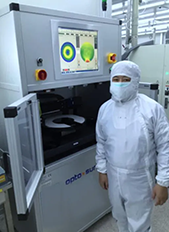
测量这一等级的表面粗糙度的常用方法是通过共聚焦显微镜 (CFM)、白光干涉仪 (WLI) 或原子力显微镜 (AFM) 进行单点或是划线测量。但这些仪器的缺点是对机械环境噪声敏感,测量时间长。
这里,我们将介绍一种新型的散射光测量方法,该方法能够在不到 30 秒的时间内测量直径300 mm整个晶圆表面。除了粗糙度,传感器还同时测量翘曲、波纹度和缺陷。同时将展现采用不同粒度研磨表面的测试结果分析。
晶圆表面加工工艺过程
极小和高密度电子产品的趋势需要先进的工艺来满足设备的厚度和热性能规格。这意味着处理后的硅晶片必须从其原始厚度超过 700 µm 减薄至 50 µm 或更小。最常见且成本相对较低的减薄方法是通过机械去除残余硅的背面研磨。晶片固定在多孔真空吸盘上,IC(集成电路)面朝下。砂轮的旋转轴与晶片的旋转轴离轴定位(距离是晶片的半径)。卡盘呈略呈圆锥形的形状,以很小的倾斜度使晶片变形,以确保砂轮在研磨过程中仅接触晶片的一半。由于卡盘的旋转和砂轮的同时旋转,在晶片表面上产生了典型的螺旋划痕图案。
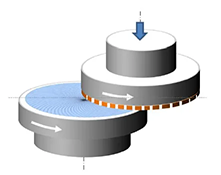
根据砂轮的粒度以及转速和进给率等加工参数,这种机械冲击是造成粗糙度、应力和诱发亚表面损伤的原因。因此,现代晶圆磨床从粗砂轮开始,先是快速去除多余硅,最后使用小粒度砂轮进行精细研磨。当减薄至 50 µm 以最大程度地减少次表面损伤和应力时,这个最终过程是绝对必要的。表面粗糙度通常应在 Ra<10 nm 甚至 1 nm 的范围内,这对机械磨床来说是一个挑战。晶圆表面的粗糙度是否太高或分布不均匀,后续的引线键合、倒装芯片组装、成型和测试等工艺步骤可能会因破裂而损坏薄芯片。除了低表面粗糙度外,切割后模具的断裂强度还取决于磨痕的方向。
当前标准测量方法的局限性是砂轮与其大量单刀刃的相互作用,与硅表面经历不均匀磨损,特别是在应用精细磨削程序时,是一个相当复杂的过程。因此,不可能通过使用 AFM、WLI 或 CFM 进行少量小区域粗糙度测量来预测研磨后整个晶片表面的质量。通常,这些标准测量方法中, AFM 的情况下,单次测量的评估面积在为 20 µm x 20 µm,在 CFM 或 WLI 的情况下为 160 µm x 160 µm。每次测量大约需要 20 s-30 s,并且需要抗振设备以避免受到环境机械噪声的影响。
OptoSurf WaferMaster 300优势
为了获得整个晶圆表面的信息,需要更快、更稳健的测量技术。散射光测量是唯一可以达到这些要求的方法,Optosurf公司基于散射光测量技术,推出一款新的测量机器(WaferMaster 300),该系统使用散射光传感器(如下图)在不到 30 S的时间内测量整个 300 mm晶片表面的粗糙度。该系统使用 OS 500 散射光技术,该技术已在用于超导和医疗应用的高质量抛光金属表面的表面测量中得到充分证明。由于传感器的特殊设计,WaferMaster 还可以测量翘曲、波纹度和缺陷。
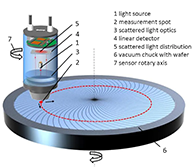
OptoSurf WaferMaster 300测量原理
WaferMaster WM 300 是一种扫描设备,其中晶片位于卡盘上,以大约 60 rpm 的速度旋转,散射光传感器垂直放置在表面上方 5 毫米处。每次旋转后,传感器向晶片中心移动一小步。根据设置,系统记录 70,000-700,000 次单次粗糙度测量,大约需要 1-10 分钟。同时,传感器测量表面斜率,这是翘曲和波纹度计算的基础。
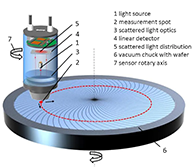
光源 (1) 以 0.9 mm 光斑尺寸 (2) 的 670 nm 红色 LED 光斑几乎垂直照射晶片表面。这是具有中等横向分辨率的快速测量的标准方法。为了获得高横向分辨率,可以打开来自具有相同波长的激光源的另一个直径为 0.03 mm 的光斑。光学器件 (3) 收集 32°角度范围内的散射光,并将其引导至线性探测器 (4)。
带有晶片 (6) 的卡盘在测量过程中连续旋转,传感器从晶片边缘线性移动到中心。随后,传感器测量整个晶圆表面,并在 30 秒内以标准方式(0.9 毫米点)对 300 毫米晶圆进行约 70.000 次单次粗糙度测量。非常重要的是传感器的额外旋转 (7),因为线性探测器应始终垂直于磨痕定向以获得最大粗糙度值。作为粗糙度参数Aq,是通过计算散射光分布的方差得出.φi是单个散射角,M是重心,p(φ)是分布曲线。
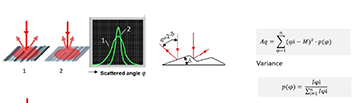
与其他散射光传感器相比,该传感器具有第二个评估通道,可通过倾斜角分析来测量翘曲和波纹度。该传感器测量镜面光(表面的 0°部分)以及由表面微结构产生的散射光。这种设置的优点是能够使用散射光分布 (5) 的重心作为表面局部几何变形的信号。了解表面的局部倾斜角度并以等距离(由编码器信号创建)连续测量表面,可以计算局部高度,并通过整合所有角度,计算表面的整个轮廓。
如下图所示,测量光束在 2 倍的局部倾斜角Ɵ下偏转。因此,散射光分布在线性探测器上偏移了角度值 M。可以通过使用第一个统计量来测量散射光分布曲线的矩。知道来自编码器的步长Δx和光学元件的焦距,就可以计算局部高度Δy并通过总结得出高度轮廓。
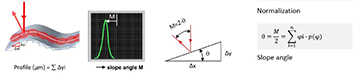
Aq与Rdq、Ra关系
Aq 的优点是与轮廓斜率参数 Rdq 的密切关系,它很好地描述了表面摩擦。为了遵循将平均粗糙度 Ra 确定为粗糙度值的 Semi 标准,通过使用共聚焦显微镜对不同晶片进行比较测量,将 Aq 参数与 Ra 相关联。由于磨削表面振幅分布的随机特性,即使在使用不同粒度的砂轮时,Aq 和 Ra 之间也有相当好的相关性。但应该考虑到 Aq 是一个更通用的参数,因为它对剖面的垂直和横向结构都有反应,而 Ra 只测量平均垂直高度。Aq 的这种特性对于表征芯片强度可能很有趣,并且应该在未来进行更详细的研究。
相关性测量 Ra (nm) = f( Aq)
在不同的区域上研究了几个晶片,磨粒尺寸从 #2000 到 #8000。此外,还测量了 Ra 值<1nm 的 CMP 抛光晶片以检查系统的准确性。为了计算 Ra 值,WaferMaster 机器中使用了拟合的相关方程。
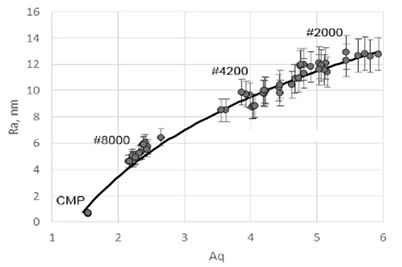
测量结果展示及分析
传感器测量散射光粗糙度值 Aq、宏观倾斜角 M(从中计算翘曲和波纹度)和强度 I。I 值与从裸晶圆散射光测量系统已知的 TIS 值相关。在粗糙度图上,颜色显示高和低粗糙度区域。光学粗糙度值Aq是散射光分布曲线的统计值(方差)。基于与已知 Ra 值的相关性,Aq 可以转换为 Ra。只要加工过程不变,这是有效的。翘曲计算基于挠度法,其中主要值是倾斜角。波纹度由高斯滤波器技术 (ISO 16610) 的翘曲导出。
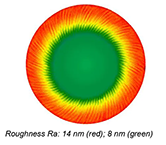
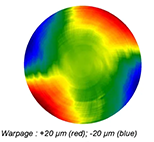
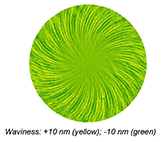
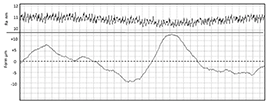
在 300 mm晶圆的 75 mm半径 (360°) 的圆周上进行轮廓测量
在下图所示,显示了 3 个晶片的粗糙度结果,每个晶片的尺寸为 300 mm。它们都用相同的砂轮(粒度#4000)磨削,但使用不同的磨床。在 25 秒内用 0.9 毫米的光斑总共进行了 40,000 次测量。除了平均粗糙度值的差异外,它还特别表明机器确实留下了自己的特征模式。详细分析磨削参数(如进给率、卡盘几何形状、旋转速度等)的解释可能会很有趣。
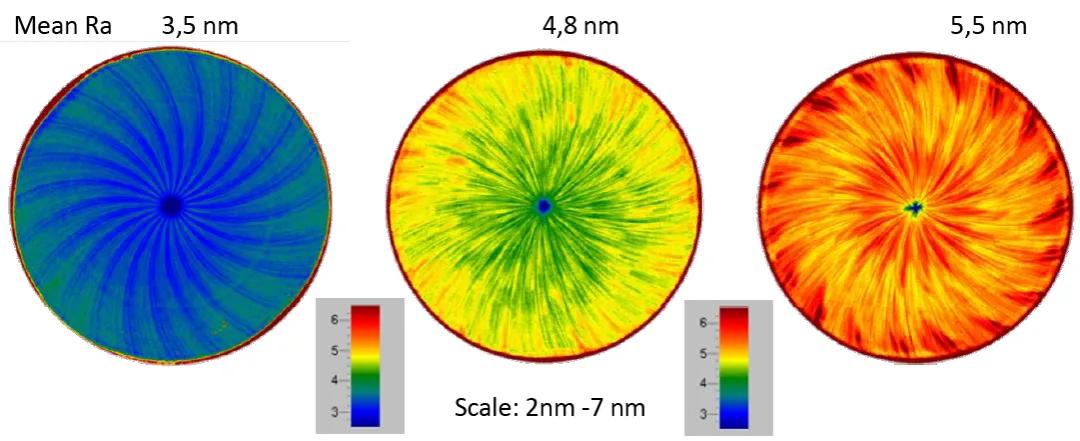
使用相同砂轮(#4000)
但不同的磨床测量 300 mm 晶片的粗糙度
在下图中可以看到同时测量 200 mm背面研磨晶片的粗糙度、形状(翘曲)和波纹度的示例。虽然砂轮的粒度也是 #4000,但平均 Ra 值要高一些。从磨痕图案可以看出,旋转是逆时针方向,从左到右改变方向。翘曲相当高,因为没有使用真空。通过应用 50 阶高通滤波器计算波纹度。过滤器在圆周上工作,这意味着中心区域比边缘和中间区域过滤得更强烈。将来会使用不同的过滤方法。波纹结构遵循粗糙模式,但也可见一些从左到右叠加的弱线状条纹。
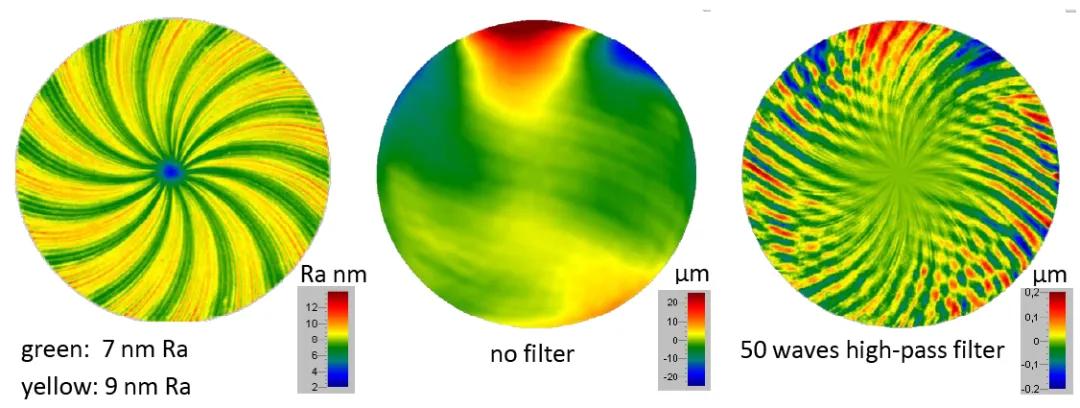
背面研磨 200 mm晶元。
左:粗糙度 Ra,中:翘曲,右:波纹度
这些条纹在下面的测量中更为突出,这是另一个 200 mm晶片但用 #2000 砂轮研磨的结果。有趣的不是由较粗的砂轮引起的更高的粗糙度,而是这里的条纹比磨痕的波纹图案更突出。从 A 到 B 评估的峰谷高度超过 1 µm,大约是磨痕波纹轮廓高度的 10 倍。
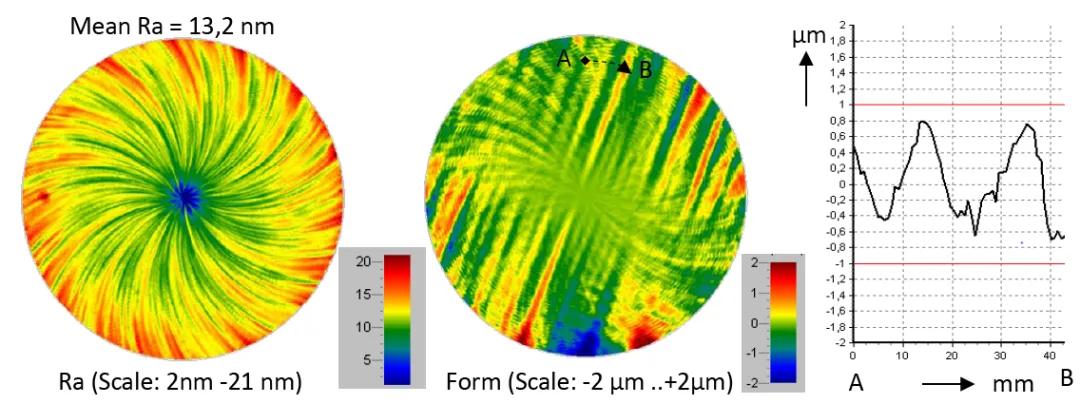
使用 #2000 粒度砂轮研磨的晶片
粗糙度 Ra(左)和波纹度图(右)
线状条纹可能是由之前的线锯过程造成的,在研磨过程后并没有消失。这可能会发生,因为在研磨过程中晶片通过真空固定在卡盘上,这使得表面暂时平坦。当晶片在研磨过程后被释放时,波纹结构恢复。此外,如果卡盘没有很好地清洁,同样的特性会产生凸起和凹坑。凹痕的示例如下图所示。300 mm抛光晶片的波纹度图覆盖有 2 个较大的凹痕和一些较小的凹痕。通过使用 0.03 毫米传感器,可以用更高的局部分辨率再次测量较大的凹坑,并在 3D 地图中表示出来。宽度在 mm 范围内,而深度不超过 1 µm。
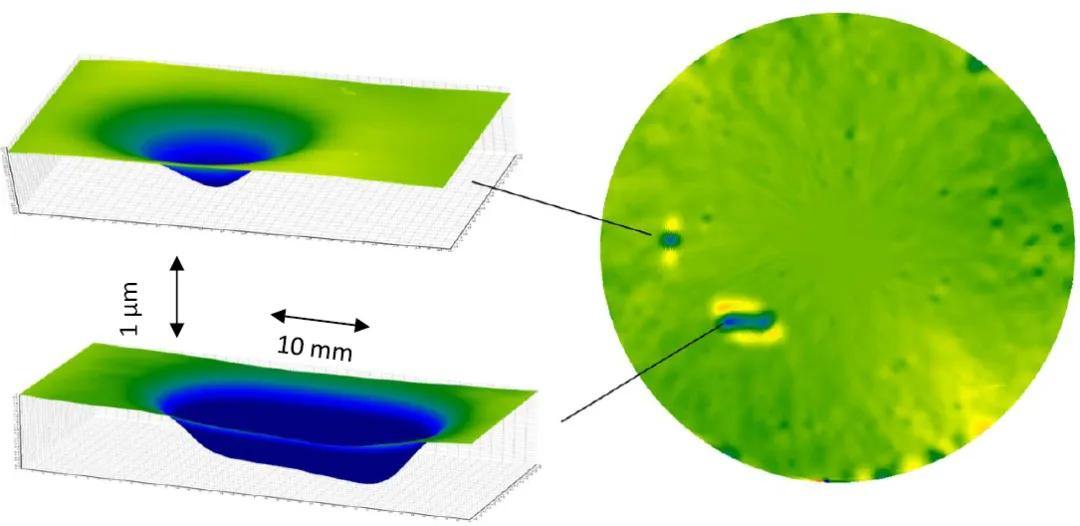
300 mm抛光晶元,带有凹痕(右 )
具有 0.03 mm 测量点的 3D 表示的高分辨率测量(左 )
高分辨率测量的另一个例子可以在下图中看到。这些测量是使用覆盖 40 mm x 20 mm区域的 x/y 扫描模块完成的,也使用 0.03 毫米的小光斑尺寸。测量值代表波纹结构(应用 25 阶高通滤波器后)。平均粗糙度为 5 nm Ra。在该部分的中心附近可以看到另一个凹痕。选定的轮廓 (a) 显示了峰谷高度约为 30 nm 的一般波纹度。重复性测量表明可以解析 1 nm 高度的结构。
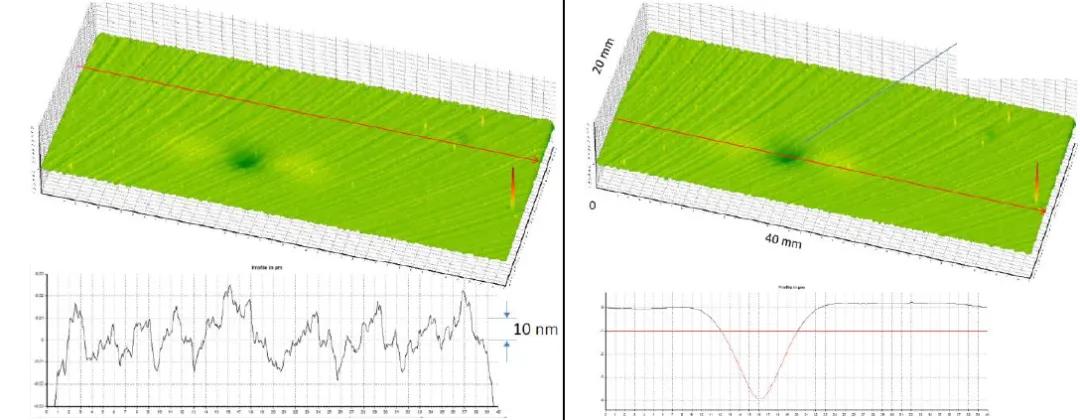
以高横向分辨率(0.03 毫米光斑)测量的精细研磨硅晶片表面
左:20 mm x 40 mm区域波纹度测量和轮廓。
右:相同的区域,但在凹痕上选择轮廓。
这使得 WaferMaster 更有趣地用于评估纳米形貌结构,以测量 CMP 工艺后的平面化质量。此外,从 3D 图形中可以看出,小点能够检测到单个缺陷(右侧的红色峰值),并且必须调查最低缺陷的极限是多少。当然,它无法与更强大的散射光系统相抗衡,特别是为前端行业的小缺陷检测而设计,但在后端流程中使用此功能就足够了。
结论
本应用案例中,提出了一种新的散射光传感器技术来测量晶片表面,特别是在背面研磨领域。该传感器通过评估散射光分布的方差 (Aq) 结合表面粗糙度测量,并另外使用偏转法来评估形状(翘曲)和波纹度。Ra 评估基于使用共聚焦显微镜的相关性测量。可以证明粗糙度测量的灵敏度下降到 Ra = 1 nm,精度为 0.1 nm。这种技术的优势在于速度(整个 300 mm晶元扫描为 25 s)和对环境机械噪声的不敏感性。粗糙度、翘曲和波纹度的全区域表示功能为表征和改进磨削工艺以及从边缘区域到中心完全检查质量开辟了新的可能性。
根据封装设计和背面研磨后工艺的敏感性,边缘到中心和沿圆周的粗糙度差异以及强烈的翘曲、波纹和缺陷会影响最终的功能和性能。分离的芯片。模具破损直接取决于粗糙度,特别是磨痕方向。因此,对背面研磨质量的快速和连续测量有助于提高后端工艺的产量。